Teaching an Old Missile New Tricks
By Charles Goldthwaite Jr., Ph.D.
ROCKET MEN: Helping the M26 improve its aim are Barry Andrews, Uday Vaidya, and Thomas Jackson.Those of us who have heard our GMCs give directions to grandma's house or our Priuses lead the way to the nearest pizza parlor know that we live in an age of increasingly sophisticated guidance systems. But when it comes to accurate directions, sometimes "close" isn't nearly good enough.
The United States military developed the global positioning system technology that makes today's in-car navigation machines possible. It still operates the most accurate version of the satellite-based network, which is especially helpful when you want to guide "smart" missiles precisely to their targets from launching pads hundreds of miles away.
In this age of smart weapons, however, the military still has plenty of dim-witted versions cluttering its arsenals. Many commonly used artillery rockets, such as the U.S. Army's M26, were designed and built prior to the guided-missile era. The United States and its allies currently have an estimated arsenal of up to 500,000 of these versatile missiles, which can be fired easily from a ground-based launch system. If only, as the Scarecrow sang inĀ The Wizard of Oz, they had brains.
Neurosurgery for Rockets
As it turns out, UAB engineers and military scientists at the Army's Aviation and Missile Research, Development, and Engineering Center at Redstone Arsenal in Huntsville have discovered a way to make that happen.
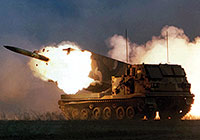
Drawing on its extensive expertise with thermoplastic composite materials, a UAB team led by Barry Andrews, Ph.D., chair of the Department of Materials Science and Engineering, and composites expert Uday Vaidya, Ph.D., is creating thin, heat-resistant aerodynamic shells to enclose trajectory-correction kits that are placed at the back of the missiles. The kits consist of four thrusters that are used to help the M26 locate its intended target.
Composite materials, a UAB specialty, are essential to the project because aluminum, the original metal selected for the correction kits, couldn't meet the necessary requirements. "A composite is intriguing because it can be tailored to fit any application by changing the matrix or the type or amount of the reinforcing fiber," Andrews observes. He points out that composites are frequently used for unique applications that demand unusually high performance, such as Formula 1 race cars, and mass-produced items that must meet a replicable standard of performance, such as tennis rackets.
The Secret is in the Mix
The material used for the trajectory-correction kit shield must meet a unique combination of requirements. "The shield will reach temperatures up to 350 degrees Fahrenheit and cannot be thicker than 0.070 inches," notes Andrews. These demands, and the need for a large number of parts, pointed the team toward a thermoplastic solution, he says. "Thermoplastics can withstand high temperatures without conducting significant heat, they're lightweight, they dampen vibrations, and they can be mass-produced quickly, cheaply, and reliably through a compression molding process."
Andrews and his colleagues have completed stress analysis on a prototype material to examine characteristics such as load-bearing capacity and to assess temperature variations during simulated flight conditions. It is now being flight-tested on actual M26 rockets, and data from these tests will help fine-tune the composition of the shield material.
If the project is successful, the Army will save millions of dollars. But for Andrews, who has spent 30 years pushing the boundaries of metals, ceramics, and plastics research at UAB, it's also another chance to "expand the limits" of his field just a little bit further.